When you enter the crew room for CAP’s Protective Coatings Department, there is a statement written at the top of the white board:
Painting is easy when you don’t know how, but very difficult when you do.
If you’ve ever painted, that may resonate with you. Painting is not easy at all! Ty Gilliland, supervisor, said the “truth on the wall” appeared about 20 years ago and no one ever admitted to writing it.
For CAP’s industrial coatings specialists, it’s a truth that is undeniable.
The first thing to note is that the men who work on the Protective Coatings crew are not painters. They are industrial coaters – journey-level craftsmen that have completed a five-year apprenticeship program. It requires 8,000 hours, including 720 hours of related education and 20 job training standards in tasks such as abrasive blasting, airless spray equipment and concrete coating. The related education consists of safety classes, classes that result in six required certifications, and technical classes throughout the first four years of the apprentice’s program.
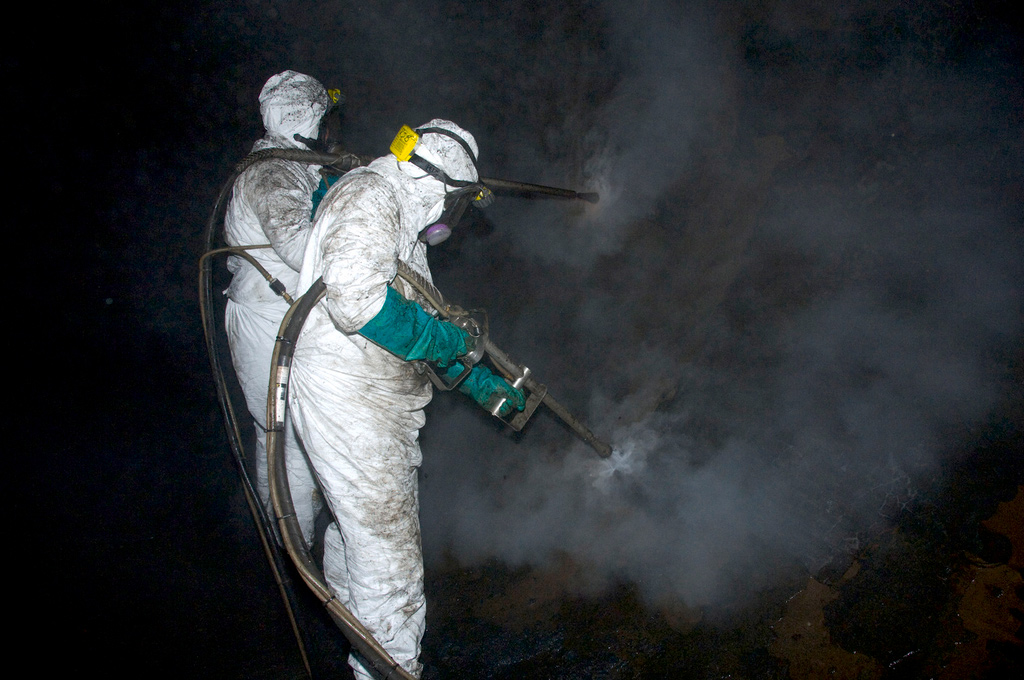

Completing the program is not an easy task, and neither is working in the field. The 10-person crew water jets, wet abrasive blasts and sand blasts. They are acutely aware of numerous hazards of the job and always put safety first. They also are extremely aware of the import role preparation plays in the success of the job.
“If a job fails, it is usually traceable to bad prep,” said Gilliland.
It is also the part of jobs that is the most time intensive. When it’s time to apply coatings, it is not one-type-for everything said Gilliland. Water based acrylics, similar to housepaint, are used for buildings, fences and interiors. Epoxy or 100% solid epoxy is used in industrial applications; locations that need protection from abrasion and corrosion. This confined space video demonstrates what some of those areas look like.
Here’s what you may not know: once a coating is applied, the thickness is measured in mils, which is 1/1000 of an inch. For acrylics, 3 mils is the goal. For epoxy, it is 6-8 mils if brushed on, 30 mils if sprayed on. To measure it while still wet, these pros use a comb-like tool. Once it is dry, an electronic tool measures it. Gilliland said that most industrial coaters can tell when they apply the coating what the measurement tool will tell them … it’s a matter of experience. And CAP’s Protective Coatings crew is full of experience! Half of the 10-person crew each have more than 22 years at CAP, a perfect situation to share experiences, pass along tips & tricks, and brainstorm innovative techniques.
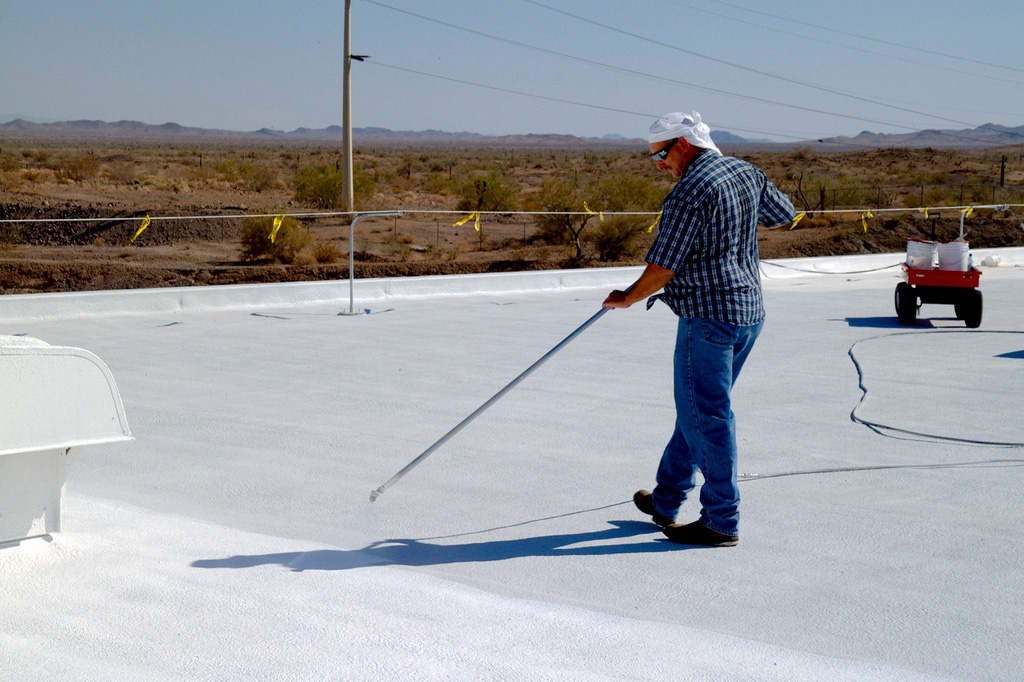
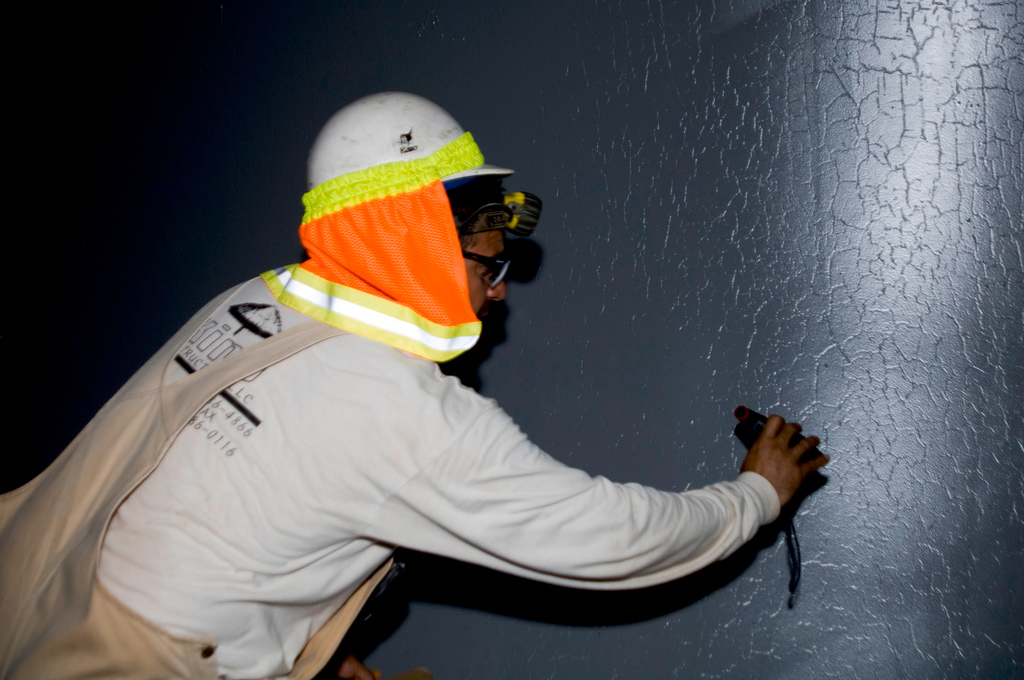
Are you wondering why the coating’s thickness matters?
“As water is pushed through pipes, it takes grit, sand, debris and shells with it, which basically means it’s experiencing wet abrasive blasting all the time, which impacts the coatings,” said Gilliland.
And water is sneaky, finding the weakest link and creeping under the coating to corrode the metal. It’s a never-ending job, but one that Ty said his crew takes great pride in doing well.
“These guys are experts and make it look easy,” said Gilliland.
Yes, they do … and it definitely is not!
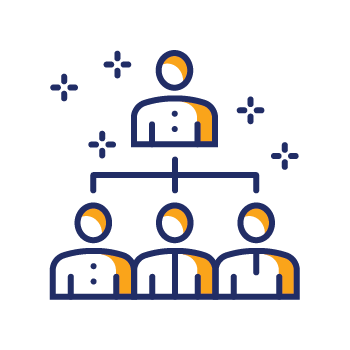
KRA: Workforce
Being a premier employer that attracts and retains an exceptional and diverse workforce